Keeping on top of track conditions from down under
When it comes to safety at BNSF, there are many layers, starting from the ground up. Our Engineering team makes sure that our railroad track and all its components – roadbed, ballast, crossties, spikes, rail and more – are well maintained and dependable.
One way we ensure track integrity is regular inspection. In addition to people doing that, we also use inspection cars, called geometry or geo cars, that survey and measure track condition as they are pulled by a locomotive and pass over the rail. We have six of these retrofitted passenger cars equipped with onboard sensors and computers travelling our system 24/7.
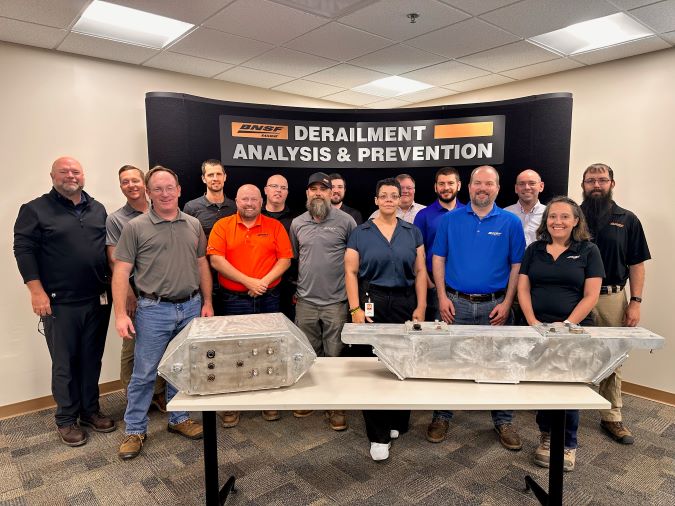
Wanting to extend our ability to cover more track more frequently, a multi-department team designed and built a locomotive-based track geometry system. It’s called ODIN (Onboard Defect Identification & Notification), a system housed in an aluminum enclosure mounted underneath a locomotive that collects and analyzes track measurement data as the locomotive is used in freight service.
“Our goal is to scale up our systems to increase our track analysis data, ultimately helping us better plan our track maintenance,” General Director Line Maintenance Planning Todd Kuhn said. “This system will use our existing locomotives as they operate at track speed – up to 70 mph – across our network.”
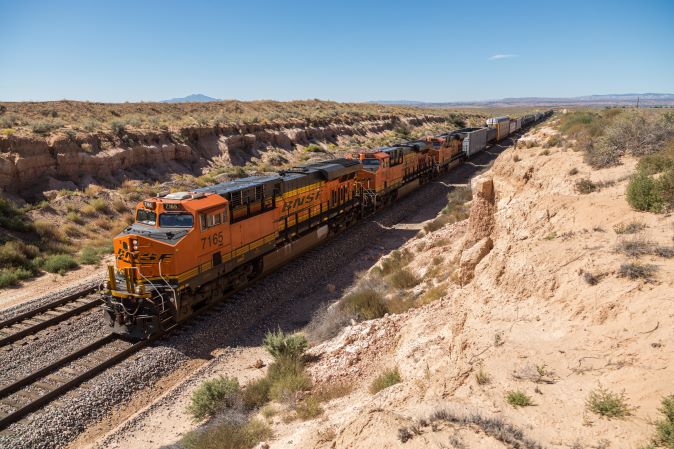
Currently ODIN has moved beyond the prototype and is in the pilot stage, with the system attached to a locomotive operating within our Technical Research & Development (TR&D) complex in Topeka, Kansas. Next it will be attached to a locomotive that is pulling revenue freight cars on our system.
TR&D designed a basic system mockup and then built a prototype; the final version looks like a metal box about the size of a large microwave oven. There were numerous design specifications, chiefly that the system could easily fit in the locomotive’s undercarriage. The version the team selected fits below the draft gear.
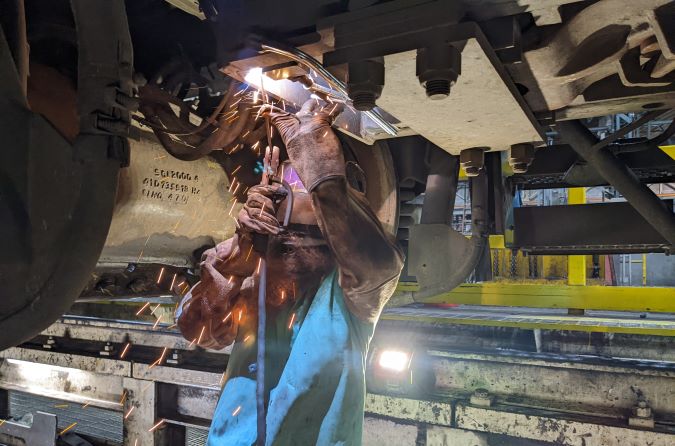
The Engineering team also had requirements of ODIN.
“We wanted to make sure that this system can collect the same data as the geo cars so we know we can count on and trust the data, so we conducted repeatability and reproducibility testing,” Charity Duran, director, Engineering & Analysis, explained.
To verify, the team compared the data collected by geo cars operating over the same section of track in the same condition and speeds with that collected by the ODIN test locomotive. “We didn’t see any deviations. Everything has looked great so far and we’re excited by the amount of data this new system will provide so we can really understand the state of our infrastructure,” Duran added.
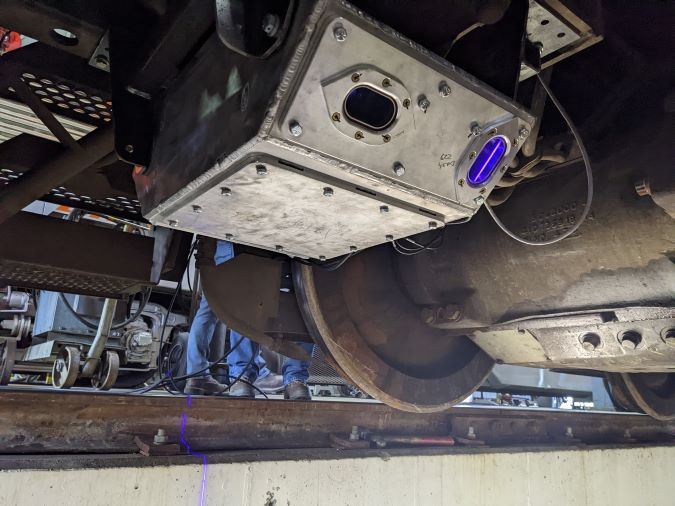
To capture the data, ODIN uses angled lasers from each side of the box to measure the gauge (distances between the two rails), cross-level alignment and track surface (the profile of the rail). The measurements are taken every foot. The information ODIN collects is processed in real-time and sent to our Engineering team via the cloud. If a defect is found, action is quickly taken to correct the issue.
“When we did the research to start building this, we needed to show that the sensors could put out the same data format and quality as the current track measurement systems on the geometry cars,” Assistant Director TR&D Darrell Krueger said. “We have proven that and now want to be able to make these systems – or as much as we can – in-house.”

The plan is to add multiple locomotive geo systems, which will complement our geo cars and other inspection methods. By having these new systems, BNSF will have more autonomous track inspection systems than the entire industry combined. (Currently there are 35 track geometry vehicles operated by all North American Class 1 freight railroads, according to the American Railway Engineering and Maintenance-of-Way Association.)
ODIN can be adapted to most types of locomotives, which is important as different types of locomotives are used in different types of service, depending on the commodity, operating conditions and geography. Additionally, because the geo cars are used primarily on our main lines, ODIN-equipped units will travel over less-frequently inspected track, like industry tracks, yard tracks and sidings.
“We’re making significant progress toward our goal of zero track-caused derailments,” Kuhn said. “This is the next step-level improvement that will help us achieve that goal.”